Introduction
Predictive maintenance is a proactive approach that anticipates potential equipment failures before they occur.
By utilizing smart software, this process becomes even more efficient and effective.
This blog aims to highlight the significance of smart software in predictive maintenance.
Predictive maintenance is a crucial strategy that helps businesses reduce downtime and increase productivity.
Smart software plays a vital role in this process by leveraging advanced analytics and machine learning algorithms.
This enables organizations to collect and analyze large volumes of data from equipment in real-time, identifying patterns and potential issues.
The purpose of this blog post is to explore the benefits of using smart software for predictive maintenance.
It will delve into how smart algorithms can determine when maintenance is needed and optimize the scheduling of repairs.
By doing so, businesses can minimize equipment failures, reduce downtime, and improve overall operational efficiency.
Smart software also enables businesses to transition from reactive to proactive maintenance practices.
Instead of waiting for equipment failures to occur, this approach allows organizations to take preventive measures.
Through continuous monitoring and analysis, potential problems can be identified and addressed beforehand, ultimately saving time and money.
Furthermore, smart software enhances the accuracy and reliability of predictive maintenance.
By automating data collection and analysis, organizations can avoid human errors and inconsistencies.
It provides real-time insights, empowering maintenance teams to make informed decisions and prioritize resources effectively.
In fact, the integration of smart software in predictive maintenance is essential for businesses looking to optimize their operations.
By using advanced analytical capabilities, organizations can detect and address equipment issues ahead of time, resulting in improved efficiency and cost savings.
Predictive Maintenance with Smart Software
Predictive maintenance is a proactive approach that uses data analytics to predict equipment failures before they occur.
It plays a significant role in various industries by providing numerous benefits.
Unlike traditional maintenance approaches, predictive maintenance focuses on preventing issues rather than fixing them after they happen.
Let’s explore some examples of industries that can benefit from predictive maintenance.
Manufacturing Industry
In manufacturing, unexpected equipment failure can lead to costly production downtime.
By utilizing predictive maintenance, manufacturers can analyze data from sensors and control systems to detect potential issues and schedule maintenance activities.
This approach helps in reducing unplanned downtime, optimizing production efficiency, and minimizing operational costs.
Energy Sector
In the energy sector, reliability is crucial for uninterrupted power supply.
Smart software can analyze real-time data from power generation equipment, such as turbines and generators, to predict potential failures.
By catching these issues early on, maintenance activities can be scheduled during planned downtime, saving on operational costs and avoiding power outages.
Transportation and Logistics
Predictive maintenance can greatly benefit the transportation and logistics industry, where any delay or equipment failure can disrupt operations.
By using smart software to monitor vehicles, trains, and planes, potential failures can be predicted.
This allows for scheduled maintenance, reducing the risk of breakdowns during transportation and improving overall reliability and customer satisfaction.
Healthcare Sector
In the healthcare sector, any equipment malfunction can risk patient safety and impact medical services.
Predictive maintenance can be used to monitor critical medical devices such as MRI machines, X-ray equipment, and ventilators.
By analyzing data from these machines, potential failures can be detected, ensuring they are repaired or replaced before causing any serious disruptions.
Oil and Gas Industry
The oil and gas industry heavily relies on large-scale infrastructure and equipment.
Predictive maintenance can help monitor pipelines, drilling equipment, and machinery, detecting potential failures before they occur.
By using smart software, operators can optimize maintenance activities, minimize downtime, and prevent costly accidents or leaks.
Traditional maintenance approaches mainly rely on fixed schedules or reactive responses to failures.
This often leads to unnecessary maintenance, increased costs, and unplanned downtime.
However, predictive maintenance takes a data-driven approach, analyzing historical and real-time data to identify patterns and predict failures before they happen.
Predictive maintenance offers several advantages over traditional methods.
It reduces unplanned downtime by allowing for proactive maintenance activities scheduled during planned downtime.
This results in increased equipment availability, improved operational efficiency, and reduced maintenance costs.
Additionally, predictive maintenance helps extend the lifespan of equipment and reduces the need for frequent replacements.
In essence, predictive maintenance using smart software is revolutionizing various industries by enabling proactive maintenance activities.
It helps prevent equipment failures, reduces downtime, and optimizes operational efficiency.
Industries such as manufacturing, energy, transportation, healthcare, and oil & gas can greatly benefit from this approach.
By utilizing data analytics and advanced algorithms, companies can stay ahead of potential issues and ensure reliable and efficient operations.
Read: Blockchain: Disruptor in Real Estate Market
Benefits of Predictive Maintenance with Smart Software
How smart software enhances predictive maintenance strategies
In the realm of industrial operations, the evolution of technology has ushered in a new era of efficiency and reliability.
One such advancement that has gained significant traction is predictive maintenance powered by smart software.
This innovative approach transcends traditional maintenance strategies by leveraging data analytics and machine learning algorithms to anticipate equipment failures before they occur.
Let’s delve into the benefits of predictive maintenance with smart software.
Smart software serves as the backbone of predictive maintenance strategies, revolutionizing how organizations manage their assets.
By continuously monitoring equipment performance and collecting vast amounts of data, these systems can identify patterns and anomalies indicative of potential failures.
This proactive approach enables timely interventions, minimizing downtime and maximizing productivity.
The advantages of using smart software for data analysis and machine learning
The advantages of employing smart software for data analysis and machine learning are manifold.
Unlike conventional methods that rely on predefined thresholds or schedules, smart software harnesses the power of predictive analytics to forecast maintenance needs accurately.
Through sophisticated algorithms, it can analyze complex data sets in real-time, providing actionable insights into equipment health and performance trends.
This predictive capability empowers organizations to optimize maintenance schedules, allocate resources efficiently, and extend the lifespan of critical assets.
Furthermore, smart software excels in its ability to detect subtle deviations in equipment behavior, serving as an early warning system for impending failures.
By continuously monitoring key parameters such as temperature, vibration, and fluid levels, these systems can flag anomalies that might go unnoticed by human operators.
This proactive identification enables prompt corrective action, averting costly breakdowns and mitigating safety risks.
How smart software can help detect and prevent equipment failures
Moreover, smart software facilitates preventive maintenance by recommending proactive measures to address potential issues before they escalate.
By analyzing historical data and predicting failure probabilities, these systems empower organizations to implement targeted maintenance strategies, such as component replacements or lubrication adjustments, precisely when needed.
This predictive foresight not only reduces unplanned downtime but also enhances overall equipment reliability and operational efficiency.
Basically, the integration of smart software into predictive maintenance practices offers unparalleled benefits for modern industries.
By harnessing the power of data analytics and machine learning, organizations can enhance equipment reliability, minimize downtime, and optimize maintenance operations.
As technology continues to evolve, embracing predictive maintenance with smart software is essential for staying competitive in today’s dynamic marketplace.
Read: Cost Analysis: Property Management Software
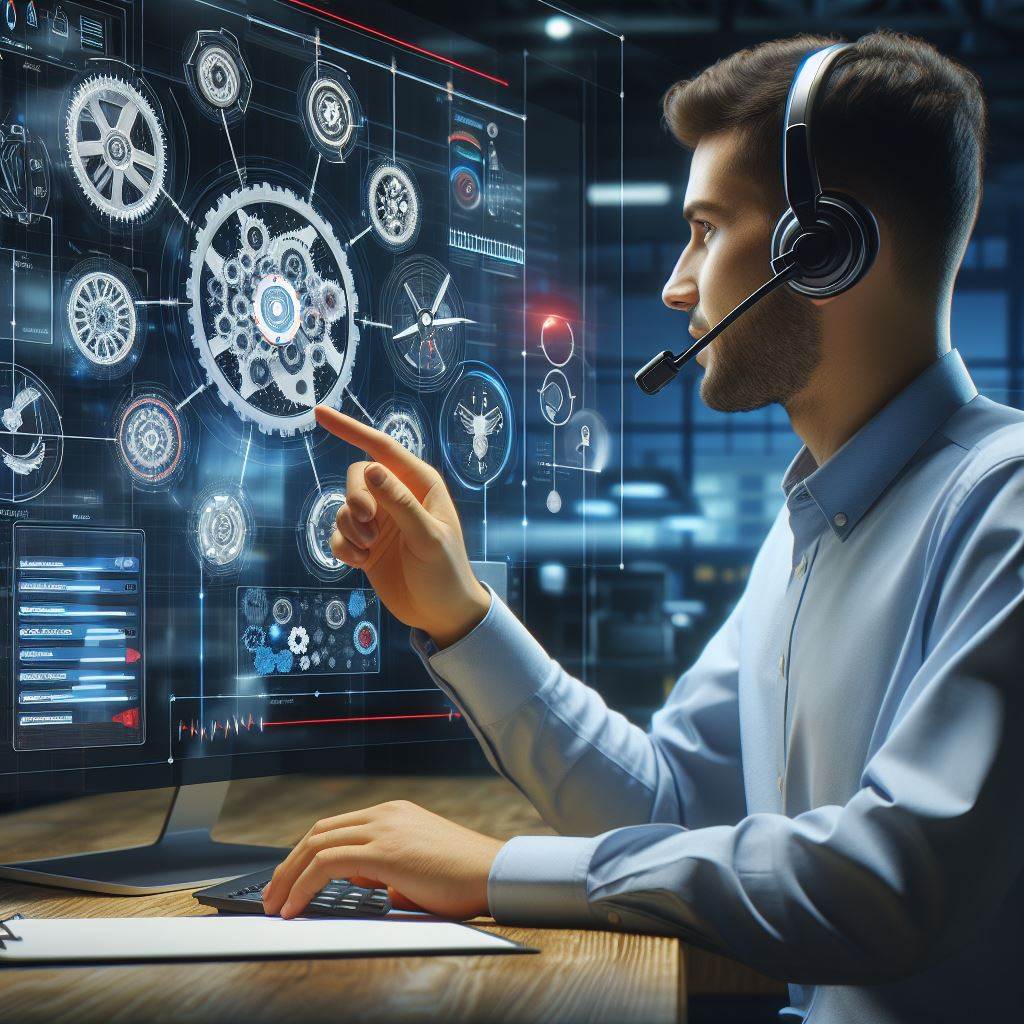
Key Features of Smart Software for Predictive Maintenance
Smart software has revolutionized the field of predictive maintenance by offering a range of advanced features.
Here, we highlight some of the key features that make smart software indispensable for predictive maintenance.
Real-time Monitoring Capabilities
One of the most crucial features of smart software is its ability to provide real-time monitoring.
This means that it can continuously collect data from various sensors and devices, allowing maintenance teams to detect anomalies and potential equipment failures as soon as they occur.
By monitoring equipment in real-time, maintenance teams can proactively identify issues and take immediate action to prevent costly breakdowns and downtime.
This feature significantly enhances the reliability and efficiency of maintenance operations.
Data Collection and Analysis
Smart software is designed to handle vast amounts of data generated by sensors, machines, and other monitoring devices.
It can collect and store this data securely, ensuring that it is readily accessible for analysis.
Moreover, smart software utilizes advanced algorithms and analytics capabilities to process this data efficiently.
By analyzing historical and real-time data, the software can identify patterns, trends, and anomalies, enabling maintenance teams to make data-driven decisions and create effective maintenance strategies.
Integration of Artificial Intelligence and Machine Learning Algorithms
Artificial intelligence (AI) and machine learning (ML) algorithms are integrated into smart software to enhance its predictive capabilities.
By leveraging AI and ML, the software can learn from historical data, identify patterns, and predict future equipment failures with a high level of accuracy.
These algorithms can also adapt and improve over time as they receive new data, making the software increasingly accurate and reliable.
The integration of AI and ML algorithms enables maintenance teams to transition from reactive maintenance to proactive and predictive maintenance, saving time and resources.
Fault Diagnosis and Prognostics
Another essential feature of smart software is its ability to diagnose faults and predict the remaining useful life of equipment.
By analyzing data from sensors and historical maintenance records, the software can identify the root cause of equipment failures and provide recommendations for repairs or replacements.
This proactive approach to maintenance helps organizations minimize unplanned downtime, optimize inventory and spare parts management, and extend the lifespan of critical assets.
Remote Monitoring and Mobile Access
Smart software often offers remote monitoring capabilities, allowing maintenance teams to access real-time data and alerts from any location.
This feature is particularly valuable for organizations with multiple sites or distributed assets.
With mobile access, maintenance technicians can receive critical alerts and notifications on their smartphones or tablets, enabling them to respond quickly and efficiently to equipment failures or abnormal conditions.
User-friendly Interface and Visualization
Smart software is designed with a user-friendly interface, making it easy for maintenance teams to navigate and interact with the system.
The software typically provides dashboards, charts, and visualizations, allowing users to interpret data intuitively.
This visualization capability helps maintenance teams gain valuable insights from complex data sets and communicate findings to stakeholders effectively.
Seamless Integration with Existing Systems
Compatibility and integration with existing systems, such as enterprise resource planning (ERP) and computerized maintenance management systems (CMMS), is a crucial feature of smart software.
Seamless integration allows organizations to make the most of their existing infrastructure, avoid disrupting workflows, and streamline maintenance processes.
Smart software for predictive maintenance offers a range of key features that revolutionize the way maintenance operations are conducted.
With real-time monitoring, advanced analytics, and AI algorithms, organizations can proactively identify and prevent equipment failures, optimize maintenance strategies, and maximize asset reliability.
By leveraging the power of smart software, maintenance teams can save time, reduce costs, and enhance overall operational efficiency.
Read: Blockchain for Faster Property Sales Process
Implementation of Predictive Maintenance with Smart Software
Steps for Implementing Predictive Maintenance with Smart Software
- Identify critical assets and determine the appropriate smart software for predictive maintenance.
- Collect historical data from the identified assets to establish a baseline for future analysis.
- Implement sensors and monitoring devices to gather real-time data on asset performance.
- Integrate the smart software with the sensor data to enable predictive maintenance analysis.
- Configure the software to establish thresholds and trigger alerts for potential issues or failures.
- Establish a feedback loop to continuously improve the predictive models based on collected data and observed outcomes.
- Train and educate maintenance personnel on how to interpret and act upon the software-generated insights.
- Regularly review and update the predictive maintenance strategy based on new data, technology advancements, and lessons learned.
Importance of Data Collection, Storage, and Analysis
Data collection is vital for predictive maintenance as it provides the basis for analysis and modeling.
Storing the collected data securely and efficiently allows for future trend analysis and model refinement.
Accurate analysis of the collected data enables the identification of patterns, anomalies, and indicators of potential asset failures.
Moreover, proper analysis helps prioritize maintenance activities and optimize resource allocation.
Setting up Predictive Models and Interpreting Results
To set up predictive models, follow these steps:
- Define the problem or failure mode to be predicted and select relevant data variables.
- Clean and preprocess the data by removing noise, outliers, and redundant variables.
- Split the data into training and testing sets to evaluate the model’s performance.
- Select and implement appropriate machine learning algorithms, such as regression, decision trees, or neural networks.
- Train the model on the training dataset and fine-tune its parameters for better accuracy.
- Evaluate the model’s performance using the testing dataset and iterate to improve its accuracy, sensitivity, and specificity.
Interpreting the results of predictive models involves
- Analyzing model metrics, such as accuracy, precision, recall, and F1 score, to gauge performance.
- Identifying important features or variables that significantly influence the model’s predictions.
- Monitoring prediction outputs and comparing them with actual asset conditions to evaluate model reliability.
- Taking appropriate maintenance actions based on model predictions to prevent failures and minimize downtime.
- Periodically retraining and updating the models as new data becomes available to ensure their relevance and accuracy.
Implementing predictive maintenance with smart software is a proactive approach that optimizes asset performance and reduces unplanned downtime.
Leveraging data collection, storage, and analysis, organizations can make informed decisions based on accurate predictions, ultimately resulting in improved operational efficiency and cost savings.
Read: Real Estate Bots: Enhancing Customer Service
Learn More: Real Estate Apps: Buying Homes Online
Case Studies and Examples
When it comes to implementing predictive maintenance with smart software, several companies have successfully embraced this technology to enhance their operations and achieve significant benefits.
Let’s explore some real-life examples:
General Electric (GE)
In an effort to optimize their maintenance processes, GE adopted predictive maintenance with the help of smart software.
By analyzing real-time sensor data, they were able to predict equipment failures before they occurred.
This proactive approach helped GE reduce downtime and increase operational efficiency.
Delta Airlines
Delta Airlines utilized predictive maintenance and smart software to monitor and analyze the performance of their aircraft engines.
By detecting anomalies in sensor data, they were able to schedule maintenance tasks more effectively, preventing unplanned maintenance events and improving overall flight reliability.
Rio Tinto
In the mining industry, Rio Tinto implemented predictive maintenance with smart software to optimize their equipment maintenance.
This approach allowed them to monitor the health of their machinery and identify potential failures early on, minimizing downtime and increasing productivity.
The Outcomes and Benefits
The successful implementation of predictive maintenance with smart software can bring numerous advantages to organizations:
Cost Reduction
By adopting predictive maintenance, companies can avoid costly equipment breakdowns and plan maintenance activities more efficiently.
This results in reduced maintenance costs and increased operational savings.
Improved Safety
Predictive maintenance helps prevent equipment failures, which can lead to accidents or safety hazards.
By identifying issues in advance, organizations can take proactive measures to ensure the safety of their employees and customers.
Enhanced Operational Efficiency
Smart software allows organizations to optimize maintenance schedules based on real-time data.
This leads to improved equipment availability, reduced downtime, and increased overall efficiency in production processes.
Overcoming Challenges
Implementing predictive maintenance with smart software may come with its fair share of challenges:
Data Integration
Integrating smart software with existing systems and data sources can be complex and time-consuming.
Companies need to ensure seamless data flow for accurate predictions and analysis.
Skill Gap
Utilizing smart software technologies requires trained personnel who can effectively analyze the collected data and interpret the predictions.
Organizations may need to invest in training programs to bridge this skill gap.
Change Management
Implementing predictive maintenance involves a shift in the traditional reactive maintenance mindset.
Organizations need to effectively communicate the benefits of this approach and gain buy-in from stakeholders to facilitate a smooth transition.
Essentially, predictive maintenance with smart software has proven to be a game-changer for many companies.
Real-life examples like General Electric, Delta Airlines, and Rio Tinto showcase the significant benefits, including cost reduction, improved safety, and enhanced operational efficiency.
While challenges like data integration, skill gaps, and change management exist, overcoming them with proper planning and resources can lead to successful implementation.
Conclusion
By using smart software for predictive maintenance, businesses can benefit in numerous ways.
It allows for proactive maintenance, reducing downtime and costs.
Staying ahead of equipment failures is crucial in maintaining efficiency and avoiding unexpected breakdowns.
We highly encourage readers to explore and adopt smart software solutions for predictive maintenance in their respective industries.
By doing so, they can improve operational reliability, optimize maintenance schedules, and enhance overall productivity.
Investing in predictive maintenance not only saves money but also helps businesses stay competitive in today’s fast-paced market.
So, don’t wait any longer. Embrace the power of smart software for predictive maintenance and take your business to new heights!