Introduction
Manufacturing is a vital industry in the United States, contributing significantly to its economy.
It encompasses various sectors, including automotive, electronics, aerospace, and chemicals.
With advancements in technology and globalization, the future of manufacturing spaces in the US is poised for transformation.
The importance of manufacturing spaces cannot be underestimated in supporting economic growth.
These spaces provide a foundation for innovation, productivity, and job creation.
They serve as hubs for research and development, fostering collaboration between industries and academic institutions.
Manufacturing spaces also play a critical role in attracting investment and driving exports.
By providing the necessary infrastructure and facilities, they enable manufacturers to produce goods efficiently and competitively.
This, in turn, contributes to the country’s trade balance and overall economic wellbeing.
Furthermore, manufacturing spaces have the potential to address societal challenges such as sustainability and resource efficiency.
By incorporating green practices and adopting advanced technologies, they can minimize environmental impact while maximizing productivity and profitability.
In the future, manufacturing spaces will undergo significant changes due to factors like automation, artificial intelligence, and additive manufacturing.
These developments will lead to improved efficiency, reduced costs, and increased customization capabilities.
However, challenges remain, including the need for skilled workers, infrastructure investments, and regulatory frameworks that support innovation.
Addressing these challenges will be crucial in ensuring a thriving manufacturing sector and sustaining economic growth.
In essence, manufacturing spaces in the US are vital for supporting economic growth.
They provide a platform for innovation, job creation, and global competitiveness.
Embracing technological advancements and addressing challenges will help shape a promising future for the manufacturing industry.
Current challenges and trends in manufacturing spaces
Increase in demand for flexible and adaptable spaces
Manufacturers are increasingly seeking manufacturing spaces that are flexible and adaptable to their changing needs.
These spaces allow companies to easily reconfigure the layout and adjust production processes as required.
The demand for flexible spaces is driven by the need for quick response to market changes and customer demands.
Manufacturers need spaces that can accommodate new technologies and equipment without extensive modifications.
Adaptable spaces enable manufacturers to efficiently utilize resources and optimize production efficiency.
Flexibility in manufacturing spaces also allows for easy integration of automation and robotics systems.
The ability to quickly scale production capacity up or down is also a significant advantage in a dynamic market.
Manufacturers that can adapt quickly to changing market conditions have a competitive edge in the industry.
Flexible spaces also promote collaboration and innovation, as they can be easily reconfigured to facilitate new ideas.
The demand for flexible and adaptable spaces in the manufacturing sector is expected to continue growing in the future.
Technology advancements influencing manufacturing processes
Technology advancements are revolutionizing the manufacturing industry and transforming manufacturing spaces.
Automation, robotics, and artificial intelligence are increasingly being integrated into manufacturing processes.
These advancements improve efficiency, productivity, and quality in manufacturing operations.
Manufacturers are utilizing smart machines and connected devices to streamline their production processes.
The Internet of Things (IoT) enables machines to communicate and share real-time data, optimizing production.
Advanced technologies also allow for predictive maintenance, reducing downtime and optimizing equipment performance.
Virtual reality and augmented reality are being used for training and simulation purposes in manufacturing spaces.
Digital modeling and simulation tools aid in design and prototyping, reducing time to market for new products.
Advanced analytics and data-driven insights help manufacturers make informed decisions and improve processes.
Technology advancements continue to shape manufacturing spaces, enhancing efficiency, flexibility, and competitiveness.
Growth of sustainable and eco-friendly manufacturing spaces
The manufacturing industry is increasingly focusing on sustainability and eco-friendly practices.
Manufacturing spaces are being designed and operated with environmental considerations in mind.
Sustainable manufacturing spaces minimize waste generation and reduce energy consumption.
Green building techniques and materials are being adopted to create energy-efficient manufacturing facilities.
Renewable energy sources like solar and wind power are being integrated into manufacturing spaces.
Water conservation techniques and efficient waste management systems are implemented in manufacturing spaces.
The use of environmentally friendly materials and technologies is promoted in manufacturing processes.
Companies are adopting sustainable supply chain practices, considering the environmental impact of their operations.
Sustainability certifications, such as LEED (Leadership in Energy and Environmental Design), are sought after for manufacturing spaces.
Sustainable manufacturing spaces not only reduce the environmental footprint but also enhance brand reputation and attract environmentally conscious customers.
The future of manufacturing spaces in the US will be characterized by increased demand for flexible and adaptable spaces.
Technology advancements will continue to influence manufacturing processes, while the growth of sustainable and eco-friendly spaces will be prioritized.
Manufacturers must adapt to these challenges and trends to remain competitive and meet the evolving needs of the industry.
Read: Hotel Sector CRE: Is It Worth Investing in 2024?
The impact of automation and robotics on future manufacturing spaces
Integration of robotic systems in manufacturing processes
- Robotic systems are increasingly being integrated into manufacturing processes to enhance efficiency.
- These systems can perform repetitive tasks with high precision, reducing human error.
- Robots can work faster and operate continuously, leading to increased productivity.
- They can handle heavy loads and work in hazardous environments, ensuring the safety of workers.
Benefits and potential challenges of automation in manufacturing spaces
- Automation in manufacturing spaces can significantly improve productivity and reduce production costs.
- It allows for faster production cycles and shorter time-to-market for products.
- Automation also enables customization and personalization of products to meet individual customer needs.
- However, there are potential challenges such as initial investment costs and maintenance of robotic systems.
- Workforce displacement and the need for retraining and upskilling also pose challenges.
Importance of upskilling workforce to adapt to automation
- With the integration of automation, the skills required in manufacturing spaces are evolving.
- Workers need to acquire new skills such as programming and operating robotic systems.
- Upskilling the workforce allows for a smooth transition to automated manufacturing processes.
- It empowers workers to take on higher-value tasks that require human creativity and problem-solving abilities.
- Continuous learning and upskilling are crucial to remain relevant in the future of manufacturing spaces.
Automation and robotics are revolutionizing the future of manufacturing spaces in the US.
The integration of robotic systems brings numerous benefits, including enhanced efficiency, increased productivity, and improved worker safety.
However, there are challenges that need to be addressed, such as initial investment costs and workforce displacement.
Upskilling the workforce is essential to adapt to automation and ensure a smooth transition to automated manufacturing processes.
By acquiring new skills, workers can embrace higher-value tasks and contribute to the continued success and growth of the manufacturing industry.
Manufacturing spaces in the US are on the brink of transformation, and embracing automation and upskilling the workforce will be key to thriving in this evolving landscape.
Read: Smart Tech in Modern Warehousing
Shift towards smart and connected manufacturing spaces
Introduction to the concept of smart manufacturing
In recent years, there has been a significant shift towards smart manufacturing in the United States.
This concept refers to the use of advanced technologies and data analytics to improve the efficiency and productivity of manufacturing spaces.
Smart manufacturing involves the integration of various components such as sensors, automation, artificial intelligence (AI), internet of things (IoT), and big data analytics.
Integration of IoT, AI, and big data analytics in manufacturing spaces
One of the key components of smart manufacturing is the integration of IoT devices.
These devices are embedded with sensors that collect real-time data from various machines and equipment.
This data is then analyzed using AI and big data analytics algorithms to identify patterns and trends.
AI technologies are used to automate decision-making processes and optimize manufacturing operations.
Machine learning algorithms can analyze large amounts of data and make predictions or recommendations to improve productivity and reduce downtime.
Big data analytics plays a crucial role in smart manufacturing by providing insights into manufacturing processes and identifying opportunities for improvement.
Analyzing large datasets can help identify bottlenecks, reduce waste, and optimize resource allocation.
Advantages of connected manufacturing spaces in improving efficiency and productivity
The shift towards smart and connected manufacturing spaces brings numerous advantages in improving efficiency and productivity.
- Real-time monitoring and predictive maintenance: IoT devices enable real-time monitoring of machines and equipment.
Predictive maintenance algorithms can identify potential issues before they cause downtime or breakdowns, improving overall equipment efficiency. - Optimized production processes: AI technologies can analyze production data and identify areas for optimization.
This includes adjusting machine settings, improving production scheduling, and ensuring the most efficient use of resources. - Improved quality control: Connected manufacturing spaces allow for continuous monitoring of production processes, enabling real-time quality control.
Any deviations from standards or product defects can be identified early on, reducing waste and improving customer satisfaction. - Enhanced supply chain management: By connecting manufacturing spaces with suppliers, customers, and other stakeholders, information can flow seamlessly across the supply chain.
This leads to better coordination, improved inventory management, and reduced lead times. - Increased agility and flexibility: Smart manufacturing enables quick adaptability to changing market demands.
By analyzing real-time data, manufacturers can make swift decisions to adjust production volumes, modify product designs, or introduce new products.
In essence, the future of manufacturing spaces in the United States is moving towards smart and connected environments.
The integration of IoT, AI, and big data analytics brings numerous advantages in improving efficiency, productivity, and overall competitiveness in the manufacturing sector.
Manufacturers embracing these technologies, adapting operations, thrive in the evolving manufacturing landscape.
Read: The Rise of E-Commerce Warehouses
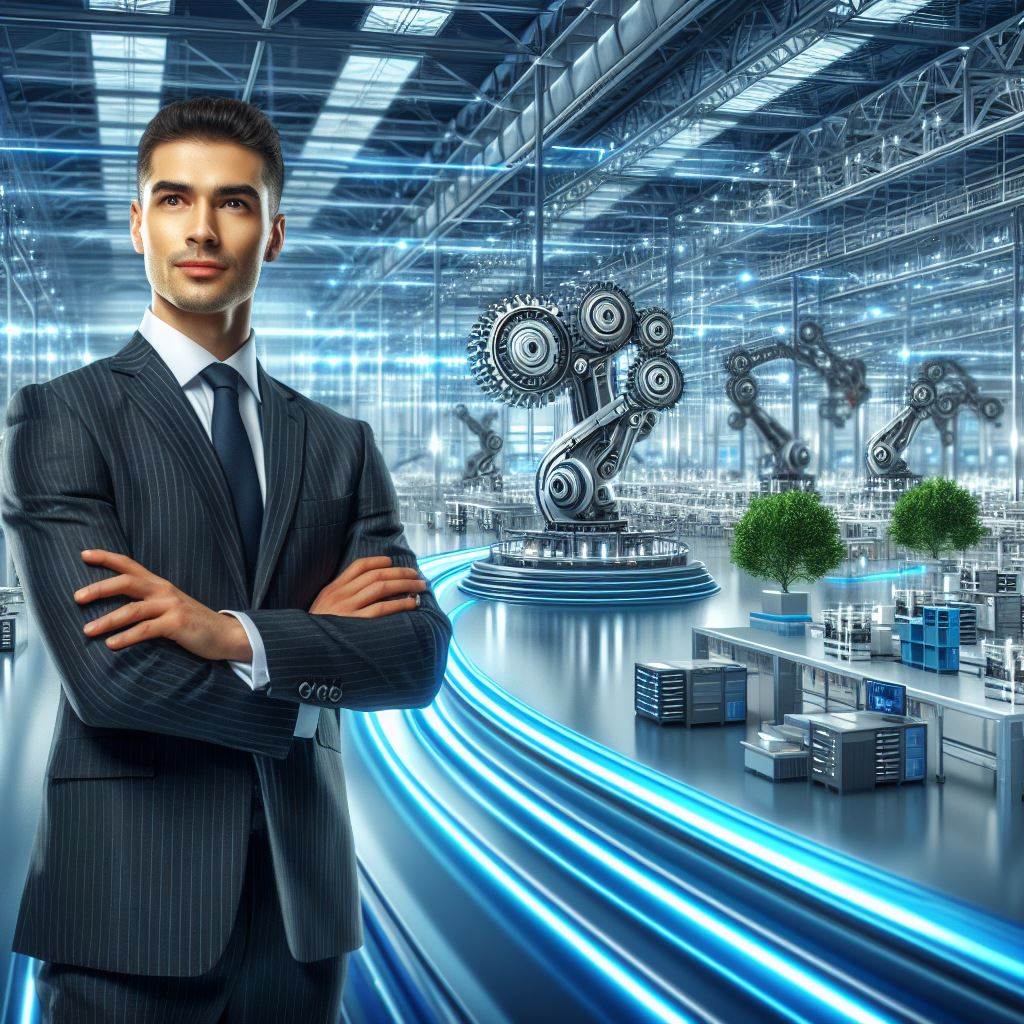
Considerations for designing future manufacturing spaces
Importance of strategic location and accessibility
- The location of manufacturing spaces is critical for their success.
- Proximity to suppliers, customers, and transportation hubs is crucial.
- Accessible locations can reduce logistical costs and improve efficiency.
- Future manufacturing spaces should be designed with easy access in mind.
Incorporation of flexible layouts and infrastructure
- Manufacturing processes are constantly evolving and changing.
- Future manufacturing spaces should be designed with flexibility in mind.
- Incorporation of modular layouts allows for easy reconfiguration of the space.
- Flexible infrastructure, such as plug-and-play systems, can accommodate changing technology.
- Future manufacturing spaces need to be adaptable to new production methods and technologies.
Need for collaboration spaces and effective communication channels
- Collaboration is key to innovation and problem-solving in manufacturing.
- Future manufacturing spaces should include dedicated collaboration areas.
- These spaces should be designed to facilitate communication and idea-sharing.
- Use of technology, such as video conferencing, can enable effective communication among teams.
- Future manufacturing spaces need to foster a culture of collaboration and open communication.
Overall, the future of manufacturing spaces in the US requires careful consideration of several factors:
- Strategic location and accessibility
- Flexibility in layouts and infrastructure
- Collaboration spaces and effective communication channels
Manufacturers can equip spaces for future challenges by considering these factors during design.
Read: Multi-Family Units: 2024’s Smart CRE Investment
Sustainable practices in future manufacturing spaces
In the future, manufacturing spaces in the US will need to embrace sustainable practices to address environmental concerns and meet the demands of a changing world.
These practices include adopting green technologies and renewable energy sources, implementing waste reduction strategies, and seeking certifications for sustainable manufacturing spaces.
Adoption of green technologies and renewable energy sources
Adopting green technologies and renewable energy sources will play a crucial role in reducing carbon emissions and minimizing the environmental impact of manufacturing processes.
By incorporating solar panels and wind turbines, manufacturing spaces can generate clean and renewable energy to power their operations.
Additionally, investing in energy-efficient machinery and utilizing smart grids will optimize energy management and promote sustainability.
Waste reduction strategies and recycling initiatives
Waste reduction strategies and recycling initiatives will also be essential in creating sustainable manufacturing spaces.
Developing comprehensive waste management plans, implementing recycling programs, and encouraging employee participation will help minimize landfill waste and promote the reuse of materials.
Incorporating circular economy principles into manufacturing processes will further contribute to waste reduction and resource conservation.
Certification programs for sustainable manufacturing spaces
Certification programs provide a means to validate sustainable practices and showcase a manufacturing space’s commitment to environmental stewardship.
Seeking certifications like LEED and implementing ISO 14001 environmental management systems demonstrate compliance with recognized standards.
Participating in voluntary sustainability initiatives allows manufacturers to access additional resources and expertise to enhance sustainability efforts.
Overall, sustainable practices in future manufacturing spaces will require a comprehensive approach.
By adopting green technologies, implementing waste reduction strategies, and obtaining relevant certifications, manufacturers can create more environmentally friendly spaces while also meeting their business needs and contributing to a more sustainable future.
Conclusion
Recap of key points discussed
- The future of manufacturing spaces in the US is evolving rapidly.
- New technologies and advancements are reshaping the industry.
- Flexibility and adaptability are crucial for manufacturing spaces to thrive.
- Collaboration and innovation are key drivers of success.
- Workforce skills need to align with the changing demands of the industry.
Importance of adapting and investing in future manufacturing spaces for economic growth
Investing in future manufacturing spaces is essential for sustaining economic growth.
It ensures competitiveness, promotes innovation, and creates job opportunities.
The evolving manufacturing landscape presents both opportunities and challenges.
Embracing automation, digitization, and sustainability can lead to increased efficiency and productivity.
However, there may be workforce adjustments and the need for constant upgrading of skills.
The future of manufacturing spaces in the US holds immense potential for economic growth.
It is vital for stakeholders to adapt, invest, and collaborate to leverage opportunities and overcome challenges in this rapidly evolving landscape.