Introduction
Energy efficiency plays a crucial role in manufacturing sites as it reduces costs and minimizes environmental impact.
Implementing energy-efficient measures brings several benefits, including increased productivity and reduced carbon emissions.
In this blog post, we will explore the importance of energy efficiency in manufacturing sites and discuss the advantages of implementing energy-efficient measures.
Energy efficiency is essential in manufacturing sites to optimize energy consumption and reduce waste.
By using energy-efficient technologies and practices, manufacturers can significantly reduce operating costs and enhance their competitiveness.
Benefits of Implementing Energy-Efficient Measures
Implementing energy-efficient measures in manufacturing sites brings numerous benefits.
Firstly, it helps enhance productivity and reduces downtime, leading to higher profitability.
Energy-efficient technology also improves the working environment, contributing to better employee satisfaction and performance.
Additionally, it reduces greenhouse gas emissions, contributing to a sustainable future and meeting environmental regulations.
Overview of the Blog Post
This blog post will delve into the topic of energy efficiency in manufacturing sites.
We will explore why energy efficiency is vital for manufacturers and the advantages they can gain from implementing energy-efficient measures.
By the end of this post, readers will have a clear understanding of how energy efficiency can improve the overall performance of manufacturing sites and contribute to a greener and more sustainable industry.
In essence, energy efficiency in manufacturing sites is of utmost importance.
By implementing energy-efficient measures, manufacturers can reduce costs, enhance productivity, and minimize their environmental impact.
In the upcoming sections, we will discuss specific energy-saving strategies and technologies that can be employed in manufacturing sites to achieve these benefits. Stay tuned for our next blog post!
Understanding Energy Efficiency in Manufacturing
Definition and Concept of Energy Efficiency
Energy efficiency in manufacturing refers to the ability of a manufacturing site to produce goods and services using the least amount of energy possible.
It involves optimizing processes, technologies, and systems to minimize energy consumption and waste.
Key Factors Influencing Energy Efficiency in Manufacturing Sites
- Technological advancements: The use of energy-efficient equipment, machinery, and automation systems can significantly improve energy efficiency in manufacturing.
- Management and employee practices: Adopting energy-saving practices, such as regular maintenance, optimized scheduling, and energy awareness programs, can contribute to better energy efficiency.
- Integration of renewable energy: Incorporating renewable energy sources like solar or wind power into manufacturing processes can reduce reliance on fossil fuels.
- Material selection and waste management: Choosing energy-efficient materials and implementing effective waste management strategies can reduce energy consumption in manufacturing sites.
- Data monitoring and analysis: Continuous monitoring, analysis, and benchmarking of energy consumption can identify areas for improvement and track energy efficiency progress.
Challenges Faced in Achieving Energy Efficiency
- Lack of awareness and prioritization: Many manufacturing sites still prioritize productivity and cost reduction over energy efficiency.
- Initial investment costs: Implementing energy-efficient technologies may require significant upfront costs, deterring some manufacturers who focus on short-term financial gains.
- Operational barriers: Complex manufacturing processes, production demands, and limited space can pose challenges to achieving energy efficiency.
- Resistance to change: Employees may resist adopting new energy-efficient practices due to lack of awareness, training, or fear of job displacement.
- Regulatory compliance: Manufacturers must navigate complex energy regulations and standards, which can vary across regions and industries.
Common Energy-Consuming Processes in Manufacturing
- Heating, Ventilation, and Air Conditioning (HVAC): HVAC systems contribute to a significant portion of energy consumption in manufacturing sites.
- Lighting: The use of inefficient lighting systems, such as traditional incandescent bulbs, can lead to unnecessary energy waste.
- Motors and drives: Motors used in machinery and equipment consume a significant amount of energy, making their efficiency crucial.
- Compressed air systems: Leakage and poor maintenance of compressed air systems result in unnecessary energy usage.
- Industrial processes: Energy-intensive processes like heat treatment, welding, and chemical reactions require careful energy management to improve efficiency.
As manufacturers seek to reduce their environmental impact and achieve sustainability goals, energy efficiency plays a pivotal role.
Understanding the definition, key factors, challenges, and common energy-consuming processes in manufacturing sites helps identify opportunities for improvement and aids in creating a more energy-efficient future.
Read: Post-COVID Trends in Warehousing
The Role of Technologies in Energy Efficiency
The impact of automation and digitalization
Automation and digitalization have revolutionized energy efficiency in manufacturing sites.
Advanced technologies allow for precise control and optimization of energy consumption.
Automated systems can monitor energy usage in real-time and identify areas for improvement.
Digitalization enables better integration of systems, leading to increased overall energy efficiency.
The use of smart sensors and IoT devices helps streamline energy management processes.
Energy management systems and monitoring tools
Energy management systems play a crucial role in monitoring and optimizing energy consumption.
These systems collect and analyze data to identify energy-intensive processes and suggest improvements.
Real-time monitoring tools allow manufacturers to track energy usage and make necessary adjustments.
Energy management software provides accurate energy reports, enabling informed decision-making.
Implementing energy-saving measures becomes easier with the help of efficient monitoring tools.
Renewable energy integration
Manufacturing sites can significantly improve energy efficiency by integrating renewable energy sources.
Solar panels, wind turbines, and geothermal systems offer sustainable alternatives to traditional energy sources.
Renewable energy integration reduces reliance on fossil fuels and lowers carbon emissions.
Energy storage systems ensure a consistent supply of renewable energy during peak demand periods.
Investing in renewable energy solutions can lead to long-term cost savings and environmental benefits.
Implementing energy-efficient equipment and machinery
Upgrading to energy-efficient equipment and machinery is essential for optimizing energy efficiency.
Energy-efficient motors, pumps, and lighting systems reduce energy consumption without compromising performance.
Using energy-saving technologies, such as variable speed drives, helps regulate energy usage based on demand.
Regular maintenance and equipment optimization ensure maximum energy efficiency throughout the manufacturing process.
Investing in energy-efficient equipment pays off in the long run through reduced energy costs and improved sustainability.
By leveraging automation, digitalization, energy management systems, and renewable energy integration, manufacturing sites can achieve significant improvements in energy efficiency.
Implementing energy-efficient equipment and machinery further enhances energy optimization efforts.
These technologies enable precise control, real-time monitoring, and informed decision-making, ultimately leading to reduced energy consumption, cost savings, and a more sustainable manufacturing industry.
Read: Green CRE Investments: The 2024 Wave
Strategies for Improving Energy Efficiency in Manufacturing Sites
Conducting energy audits and assessments
Conduct regular energy audits and assessments to identify energy efficiency opportunities in manufacturing sites.
This will help identify areas where energy consumption can be optimized and improved.
Analyzing energy consumption patterns and identifying areas for improvement
Analyze energy consumption patterns by monitoring energy usage in different manufacturing processes.
Identify areas with high energy consumption and find ways to reduce energy wastage and increase efficiency.
Implementing energy-efficient lighting solutions
Replace traditional lighting fixtures with energy-efficient alternatives such as LED lights.
Implementing motion sensors and timers can also help reduce energy consumption by automatically turning off lights when not needed.
Optimizing energy management practices
Utilize advanced energy management systems to optimize energy usage in manufacturing sites.
Monitor and control energy-consuming equipment and processes to ensure they operate at maximum efficiency.
Employee engagement and training on energy-saving practices
Involve employees in energy-saving initiatives by providing training and raising awareness about the importance of energy efficiency.
Encourage and incentivize employees to adopt energy-saving practices in their daily activities.
Implementing these strategies can help manufacturing sites significantly improve energy efficiency and decrease energy costs.
By conducting energy audits and assessments, businesses can identify areas where energy consumption can be optimized.
Analyzing energy consumption patterns allows businesses to pinpoint areas for improvement and implement targeted solutions.
Introducing energy-efficient lighting solutions and optimizing energy management practices can further reduce energy waste.
Additionally, engaging employees and providing training on energy-saving practices can create a culture of energy efficiency within the organization.
Read: Tax Incentives in Industrial Real Estate
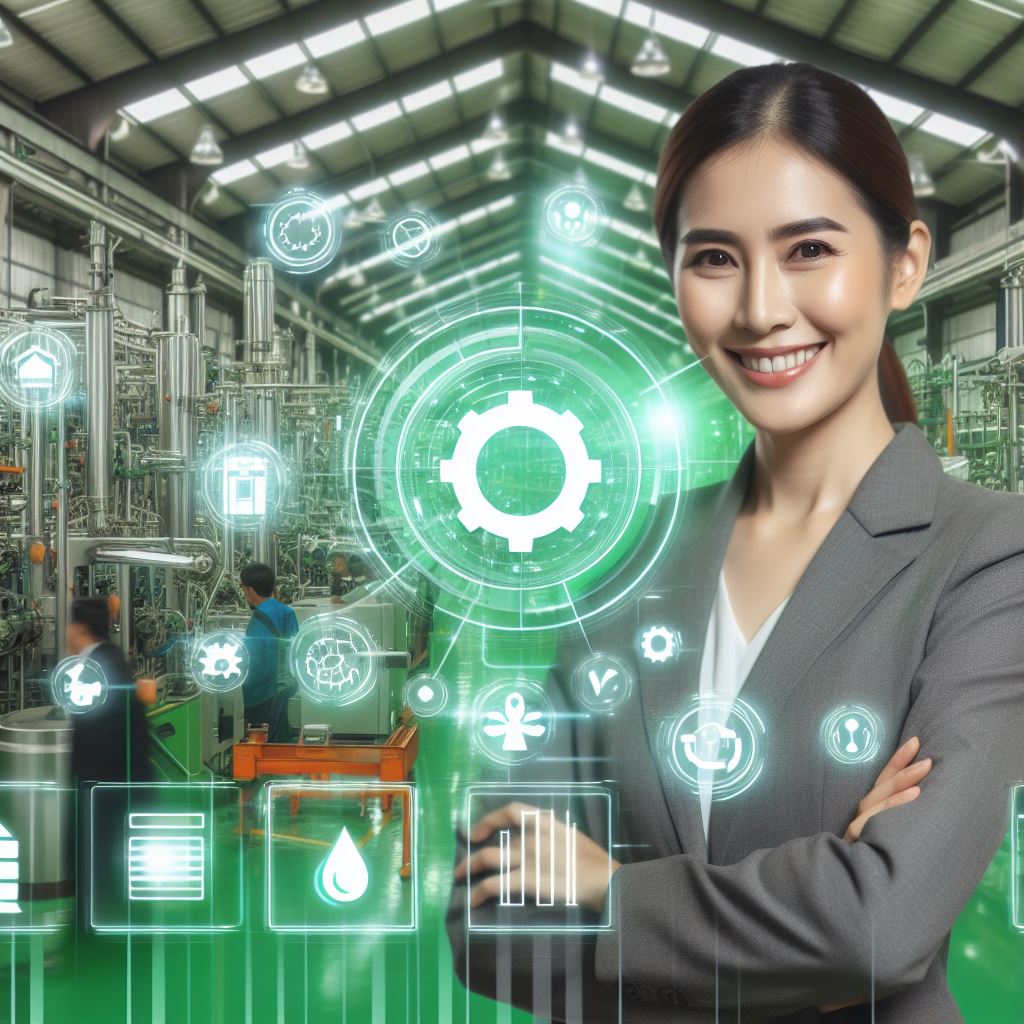
Government Incentives and Policies
Overview of government programs promoting energy efficiency
Government programs play a crucial role in promoting energy efficiency in manufacturing sites.
These programs aim to educate manufacturers about the benefits of energy-saving practices and provide support in implementing them.
By partnering with government initiatives, manufacturers can gain access to resources, expertise, and funding opportunities to improve their energy efficiency.
One such program is the Energy Star program, led by the Environmental Protection Agency (EPA) and the Department of Energy (DOE).
This program provides manufacturers with energy-saving guidelines and certifications.
Manufacturers can qualify for the Energy Star label, indicating their commitment to energy efficiency.
Additionally, the Department of Commerce offers the Manufacturing Extension Partnership (MEP), a program that assists manufacturers in improving their overall operations, including energy efficiency.
MEP centers provide technical expertise, training, and resources to help manufacturers reduce energy consumption and streamline their production processes.
Tax incentives, grants, and loans available to manufacturers
To incentivize manufacturers to invest in energy-efficient technologies, the government offers a range of tax incentives, grants, and loans.
These financial opportunities help manufacturers offset the initial costs associated with implementing energy-saving measures.
Tax incentives allow manufacturers to deduct a portion of their energy-efficient equipment’s cost from their taxes.
The government offers tax credits, rebates, and accelerated depreciation for qualifying energy-efficient investments.
Grants provide direct funding to manufacturers for energy efficiency projects.
Manufacturers can apply for grants to cover expenses related to energy audits, equipment upgrades, or process improvements that enhance energy efficiency.
Loans facilitate access to capital by offering favorable borrowing terms for manufacturers investing in energy-efficient technologies.
These loans often have lower interest rates or longer repayment periods to support manufacturers in adopting sustainable practices.
Compliance with energy efficiency standards and regulations
Government regulations set energy efficiency standards that manufacturers must follow.
These standards serve as benchmarks for energy consumption and help reduce greenhouse gas emissions.
For example, the Department of Energy sets minimum efficiency standards for various appliances and equipment used in manufacturing processes.
Manufacturers must ensure their equipment meets these standards to comply with regulations.
Manufacturers may also need to comply with building codes and regulations related to energy efficiency.
These codes specify requirements for insulation, lighting, and HVAC systems to reduce energy waste in manufacturing facilities.
To enforce compliance, the government conducts regular audits and inspections to ensure manufacturers adhere to energy efficiency standards.
Non-compliance can result in penalties, fines, or even legal actions.
In summary, government incentives and policies play a vital role in promoting energy efficiency in manufacturing sites.
Through programs, financial support, and regulations, the government encourages manufacturers to adopt energy-saving practices, reducing their environmental impact and improving overall operational efficiency.
By taking advantage of these opportunities, manufacturers can contribute to a more sustainable future while driving their own productivity and profitability.
Read: Self-Storage CRE: 2024’s Lucrative Niche
Success Stories and Case Studies
Real-life examples of successful energy efficiency initiatives in manufacturing
- ABC Company: ABC Company implemented a comprehensive energy management system that resulted in a 15% reduction in energy consumption.
- XYZ Manufacturing: XYZ Manufacturing upgraded their lighting system to LED bulbs, resulting in a 30% decrease in energy usage.
- Mega Motors: Mega Motors conducted an energy audit and identified areas of improvement, leading to a 25% reduction in energy costs.
These success stories demonstrate that energy efficiency initiatives can bring substantial benefits to manufacturing sites.
By implementing various strategies, these companies have not only reduced energy consumption but also saved costs, increased productivity, and improved their environmental footprint.
Lessons learned and best practices
- Set clear energy efficiency goals: The success stories above highlight the importance of setting specific targets to guide energy efficiency initiatives.
- Conduct energy audits: Performing regular energy audits helps identify areas with the highest potential for improvement.
- Engage employees: Encouraging employee participation and awareness is crucial for successful energy efficiency initiatives.
- Utilize advanced technologies: Companies that have integrated advanced technologies, such as smart meters and energy management systems, have achieved significant energy savings.
- Continuous monitoring and optimization: Regular monitoring and optimization of energy consumption enable companies to uncover additional saving opportunities.
- Collaborate with industry partners: Sharing best practices and collaborating with industry partners can accelerate the adoption of energy efficiency measures.
- Integrate renewable energy sources: Incorporating renewable energy sources like solar panels or wind turbines can further reduce reliance on non-renewable energy.
- Invest in employee training: Providing training on energy-efficient practices ensures that employees are equipped with the necessary knowledge and skills to contribute to energy savings.
- Monitor and report energy performance: Keeping track of energy performance and reporting it transparently helps organizations stay accountable and continuously improve.
- Communicate success internally and externally: Celebrating energy efficiency achievements within the organization and sharing them with the public can inspire others to follow suit.
By implementing these best practices and learning from successful case studies, other manufacturing sites can effectively improve their energy efficiency and reap the associated benefits.
Overall, energy efficiency initiatives in manufacturing sites have proven to be highly successful, with numerous companies achieving significant reductions in energy consumption and costs.
These success stories demonstrate that with proper planning, employee engagement, and adoption of best practices, manufacturing sites can pave the way for a more sustainable future while enhancing their competitiveness in the market.
Conclusion
Energy efficiency in manufacturing sites is paramount for sustainability and cost reduction.
By optimizing energy usage, businesses can enhance their competitiveness and minimize their environmental footprint.
Manufacturers play a pivotal role in driving energy-efficient practices.
Embracing sustainability not only benefits the planet but also boosts operational efficiency and long-term profitability.
It’s imperative for companies to integrate energy-saving initiatives into their core strategies.
Engaging in dialogue and knowledge-sharing is crucial for advancing energy efficiency in manufacturing.
Let’s foster a community where experiences and challenges are openly discussed.
Together, we can identify innovative solutions and overcome obstacles to create a more sustainable future for the manufacturing industry.
Share your insights and join the movement toward a greener, more efficient manufacturing sector.