Introduction
3D Printing: 3D printing has emerged as a groundbreaking technology that has the potential to revolutionize various industries, including construction.
This innovative process involves creating three-dimensional objects by depositing materials layer by layer based on digital designs.
It offers numerous advantages, such as cost-effective production, customization options, and enhanced efficiency.
In the construction industry, 3D printing has already started to make its mark.
The importance of this technology lies in its ability to streamline the building process, which traditionally involves complex techniques and significant manpower.
By utilizing 3D printing, construction projects can be executed more efficiently, saving time and resources.
The current state of 3D printing in construction in the United States is gaining traction.
Organizations and researchers are actively exploring its potential to construct buildings, infrastructures, and even habitats on other planets.
The use of 3D printing in construction projects has already demonstrated its capabilities, showcasing intricate designs, material efficiency, and rapid construction.
US-based companies and institutions have made significant strides in developing 3D printing solutions for construction.
They have pioneered large-scale 3D printers capable of constructing entire houses, bridges, and other structures.
Research is ongoing to optimize construction materials, improve printing techniques, and ensure regulatory compliance.
In the coming years, 3D printing in the construction industry is poised to disrupt traditional building methods, offering cost-effective, sustainable, and more time-efficient solutions.
As the technology continues to evolve, the potential for faster, cheaper, and more innovative construction projects will become a reality.
Evolution of 3D printing in the construction industryEarly Developments and Challenges
The journey of 3D printing in the construction industry began with ambitious dreams and significant hurdles.
In the early 2000s, pioneers faced challenges such as material limitations, scale constraints, and cost barriers.
Initial attempts were often experimental, focusing on small structures and basic designs.
The technology’s potential was clear, but refining the process demanded innovative solutions.
Advancements in 3D Printing Technology
As the years progressed, the construction industry witnessed remarkable strides in 3D printing technology.
Breakthroughs in materials, like advanced concrete blends and composite polymers, enhanced the durability and versatility of printed structures.
Scaling up became possible, with printers capable of constructing entire buildings. Precision and speed also improved, with intricate designs and complex architectural features now within reach.
The integration of robotics and automation played a pivotal role in streamlining the construction process.
Automated 3D printers, guided by sophisticated algorithms, could optimize material usage and reduce waste.
This not only contributed to environmental sustainability but also lowered overall project costs.
Successful Projects and Case Studies
The turning point for 3D printing in construction arrived when high-profile projects showcased its potential.
Iconic structures like affordable housing units, commercial buildings, and even emergency shelters emerged as testaments to the technology’s capabilities.
One notable success was the “Green Horizon Project,” a sustainable housing initiative that utilized cutting-edge 3D printing techniques.
By combining recycled materials with advanced printing technology, the project achieved unprecedented efficiency in construction time and cost.
This success catalyzed a wave of interest and investment, propelling the industry towards mainstream acceptance.
Case studies also demonstrated the adaptability of 3D printing to various environments.
From arid regions to urban landscapes, the technology proved its versatility in addressing diverse construction challenges.
In 2024, the US stands on the cusp of a construction revolution, with 3D printing at its forefront.
The evolution from early experiments to large-scale, efficient projects showcases the resilience and potential of this transformative technology.
As it continues to redefine the landscape of building construction, the horizon for 3D printing appears limitless.
Read: Smart Tech in Commercial Construction: A 2024 Guide
Potential benefits of 3D printing in US construction
In the dynamic landscape of construction, the advent of 3D printing is ushering in a new era of efficiency and innovation.
As we delve into the potential benefits of 3D printing in US construction, the transformative impact becomes evident across various facets.
Cost Efficiency and Reduced Labor Requirements
Traditional construction methods often involve significant labor costs and resource-intensive processes.
With 3D printing, the game changes.
The precision and automation intrinsic to this technology significantly reduce the need for extensive manual labor.
This not only slashes expenses but also mitigates the risk of human errors, resulting in more cost-effective and reliable construction.
Decreased Construction Time and Improved Project Scheduling
Time is of the essence in the construction industry, and 3D printing emerges as a time-saving marvel.
The rapid layer-by-layer construction process enables projects to be completed at an accelerated pace compared to conventional methods.
Tighter project schedules become manageable, and the timely delivery of structures becomes a hallmark of 3D printing’s prowess in the construction realm.
Increased Design Flexibility and Customization Options
The versatility of 3D printing transcends the limitations of traditional construction design.
Architects and builders can now explore intricate designs and complex structures that were once deemed impractical.
This newfound flexibility allows for unprecedented customization options, empowering stakeholders to bring their unique visions to life with greater ease and precision.
Sustainability and Waste Reduction
Sustainability is a cornerstone of modern construction practices, and 3D printing aligns seamlessly with this ethos.
By utilizing precisely measured materials, 3D printing minimizes waste, contributing to a greener construction landscape.
Additionally, the technology enables the use of eco-friendly materials, further reducing the environmental footprint of construction projects.
In essence, the potential benefits of 3D printing in US construction are manifold, promising a revolution that transcends traditional norms.
From cost savings to sustainability, the impact is not just practical but visionary, heralding a future where buildings are not just constructed but crafted with unparalleled precision and efficiency.
Read: Tenant Improvement Allowances 101
Current barriers and challenges
As the United States witnesses a transformative wave in construction through 3D printing, several challenges impede the seamless integration of this groundbreaking technology.
These barriers are not merely technical but extend into regulatory, infrastructural, and societal realms.
Regulatory and Legal Considerations
The foremost hurdle is the intricate web of regulations governing construction practices.
While 3D printing promises speed and cost-efficiency, ensuring compliance with existing building codes demands a delicate balancing act.
Regulatory bodies are grappling with updating guidelines to accommodate this novel technology without compromising safety standards.
A lack of standardized protocols for 3D-printed structures remains a substantial challenge, hindering widespread adoption.
Infrastructure and Industry Adoption
The slow pace of infrastructure development poses another obstacle.
Traditional construction methods have deep roots, and transitioning to 3D printing requires a paradigm shift.
Limited access to advanced additive manufacturing machinery and materials adds to the industry’s reluctance to embrace this innovative approach.
A comprehensive upgrade of construction infrastructure and increased investment in additive manufacturing technology are imperative for a smoother transition.
Skill Gap and Workforce Readiness
The advent of additive manufacturing demands a highly skilled workforce proficient in both digital technologies and construction.
However, there exists a significant gap in the availability of trained professionals.
Bridging this divide requires strategic initiatives in education and training programs, ensuring that the industry has a workforce well-versed in the nuances of additive manufacturing technology.
Public Perception and Acceptance
Public perception plays a pivotal role in the success of any technological revolution.
Skepticism and uncertainty surround the safety and durability of 3D-printed structures.
Building trust through transparent communication, showcasing successful projects, and dispelling misconceptions are vital steps in gaining public acceptance.
Addressing these challenges head-on is crucial to ushering in a new era of construction through additive manufacturing.
Collaborative efforts between the government, industry players, and the public will be pivotal in overcoming these barriers and redefining the future of building in the United States.
Read: Evaluating Commercial Lease Offers
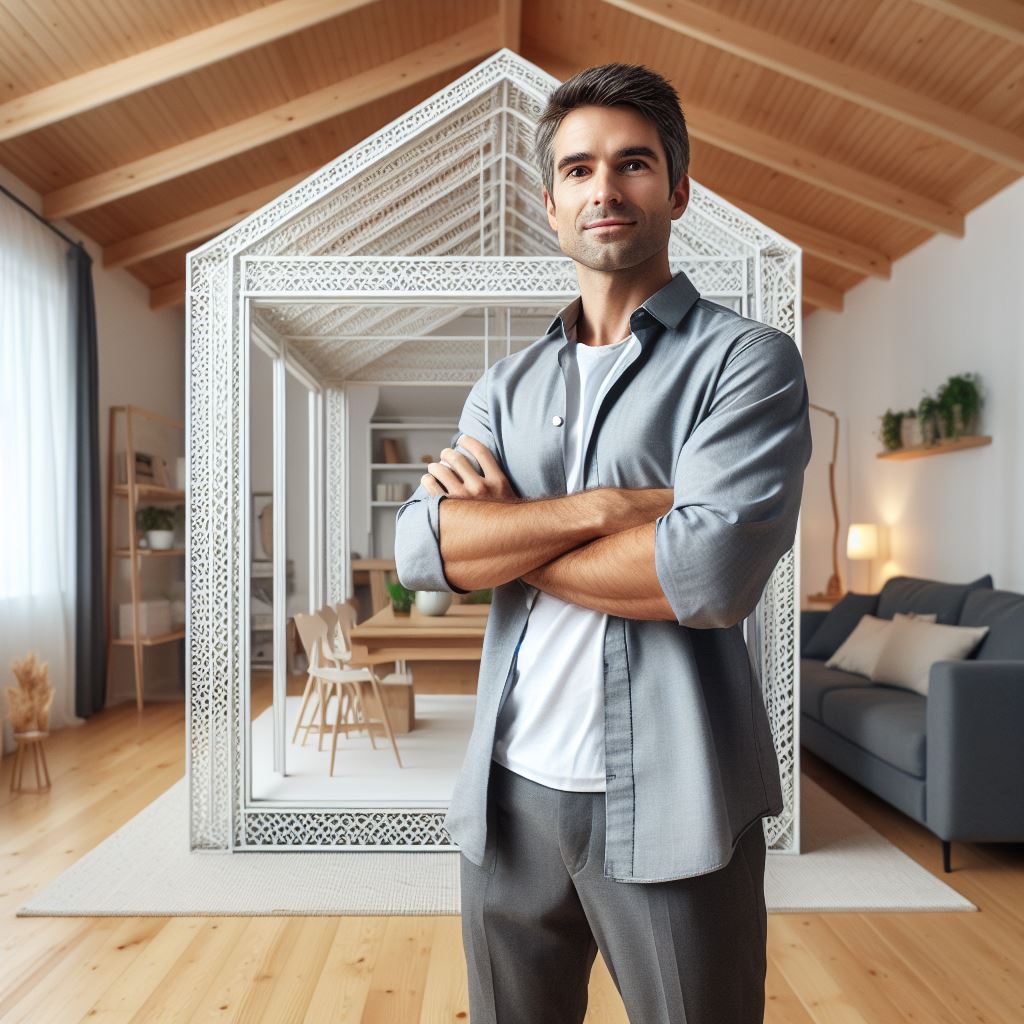
The Future of US 3D Printing in Construction (2024)
Projected Growth and Market Opportunities
In the year 2024, the US additive manufacturing industry is expected to experience substantial growth.
This growth will be driven by the increasing demand for cost-effective and sustainable construction solutions.
With the ability to create complex designs and structures quickly, additive manufacturing technology will revolutionize the construction sector.
This innovation will open up new market opportunities and attract further investments in the industry.
Collaboration between Technology Firms and Construction Companies
To fully leverage the potential of 3D printing in construction, collaboration between technology firms and construction companies is crucial.
These partnerships will combine expertise in both fields, enabling the development and implementation of advanced printing techniques.
By working together, these companies will overcome technical challenges and optimize the use of 3D printing technology in construction projects.
This collaboration will also foster innovation and create a competitive edge for both sectors.
Potential Integration with Other Emerging Technologies (AI, IoT, etc.)
The future of US 3D printing in construction lies not only in the technology itself but also in its integration with other emerging technologies.
Artificial intelligence (AI) and the internet of things (IoT) will play a significant role in advancing the capabilities of 3D printing.
By harnessing AI algorithms and IoT sensors, construction projects can be monitored and optimized in real-time, leading to increased efficiency and safety.
Integration with these technologies will enable the creation of smart buildings and infrastructure that are sustainable and responsive to changing needs.
Impact on Employment and Job Market
The widespread adoption of additive manufacturing in construction will inevitably have an impact on employment and the job market.
While some traditional construction jobs may be replaced by automated systems, new employment opportunities will emerge.
Skilled technicians and engineers will be needed to operate and maintain 3D printers, design complex structures, and oversee construction projects.
The shift towards advanced technologies will require upskilling and retraining of the workforce to ensure they can adapt to the changing demands of the industry.
Overall, the adoption of additive manufacturing technology in construction will transform the job market, creating a need for a more technologically proficient workforce.
All in all, the future of US additive manufacturing in construction looks promising.
The industry is projected to experience significant growth and open up new market opportunities.
Collaboration between technology firms and construction companies will be essential to fully harness the potential of 3D printing.
Integration with other emerging technologies, such as AI and IoT, will further enhance its capabilities.
While the adoption of 3D printing may impact employment, it will also create new jobs and require the upskilling of the workforce.
The future of US 3D printing in construction is exciting, and its potential to revolutionize the industry is immense.
Read: Luxury Commercial Spaces: 2024 Data
Conclusion
Throughout this blog post, we have explored the revolutionary potential of 3D printing in the construction industry in the United States by 2024.
We discussed the advancements in technology and its ability to streamline the building process.
We also talked about the cost-effectiveness and sustainability of 3D printing, with reduced material waste and lower labor costs.
Additionally, we highlighted the speed and precision achieved through this innovative technique.
Considering these advantages, it is crucial for construction companies and stakeholders to further explore and adopt 3D printing technology.
By doing so, they can enjoy improved efficiency, reduced costs, and increased sustainability in their projects.
Investing in research and development, training and collaboration with experts in the field will be essential to fully utilize the potential of 3D printing in the construction sector.
In the end, the revolutionary impact of additive manufacturing on the construction industry in the United States cannot be underestimated.
This technology has the capability to transform the way buildings are designed, constructed, and maintained.
By embracing additive manufacturing, the construction industry can revolutionize the traditional building methods, resulting in faster project completion, reduced costs, and improved sustainability.
The wave of change brought by additive manufacturing is imminent, and it is up to the industry to fully embrace and explore its potential in order to stay ahead in the competitive market of building and construction.